1. When measuring HVAC coils, performance has very little to do with accurately measuring for replacement coils. Fitting the coil in the existing space with the least amount of labor has everything to do with measuring a coil. If you duplicate the coil in almost every respect, the performance will match and take care of itself. New is always more efficient than old.
2. If you’re ever in doubt about a dimension, smaller is always better than bigger. You can always “safe off” around any coil as long as you can fit it in the space. If a coil is too big, it makes a really ugly coffee table in your shop. Too big is the enemy of measuring coils.
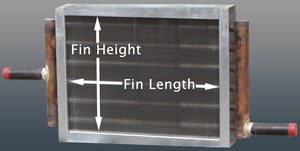
3. The fin height and fin length are not the determining factors in measuring a coil. The overall casing dimensions are the most important, and you work backwards to determine fin dimensions.
4. The depth of any coil is the total casing depth in the direction of airflow. The height is the number of tubes high in any row. Depth is a function of rows deep and height is a function of tubes in a row.
5. Overall length (OAL) is not the fin length and it’s not the casing length. It is the length from the return bends to include the headers that are inside the unit. Again, it is necessary to work backwards to get the other dimensions once you know this critical dimension.
6. Circuiting is the number of tubes connected to the supply header. Generally, you just want to count the number of tubes connected to the header and that will tell you whether it’s full, half, or even a double circuit. It does not matter how the return bends are configured. Your goal is to count the number of supply tubes and all performance is based on that.
7. Fins are measured in fins per inch. Hold a tape measure up to the coils and count the number of fins in one inch. If you can’t get in to take the measurement, a safe rule of thumb is 10-12 fins/inch. That will work on almost every coil. The exception to that rule is a condenser coil. 14-16 fins/inch on a condenser coil is usually pretty safe.
8. Connection locations are difficult only if you are using the existing piping in the system (which are welded). Copper piping is brazed and can be changed easily. If a system is old and the piping is being replaced as well as the coil, the connection location is not a major deal. It’s very easy to match up!
9. With replacement coils, the concept of “left hand vs. right hand” doesn’t actually exist. Connections are “top left-bottom right” or vice versa. Ideally, all coils should be counter-flow which means that the water and air flow in opposite directions. The air hits row one first and the water is piped into row eight first. However, there are lots of installations that are piped backwards, and they work just fine. Just match them up, and the coil’s performance will be equal to the old coil.
10. Connections are not measured from the top of the header! They are measured from the top of the casing to the centerline of the connection. Or the bottom of the casing to the centerline. You need a point of reference, and the header height can be anything just as long as it doesn’t stick above or below the casing height.
All of the above “suggestions” or “secrets” are in no particular order. They are just things that you should know to ensure that you are selecting the correct replacement coil. While most seem like common sense, your best bet is to talk with the sales team at Capital Coil & Air, who can walk your through the entire process and help you to fill out coil drawings when trying to measure the dimensions.
RELATED POSTS
Replacement HVAC Coils: 10 Common Ordering Mistakes